ACTUAL PICTURES OF THE FACTORY CONTROL CABINET
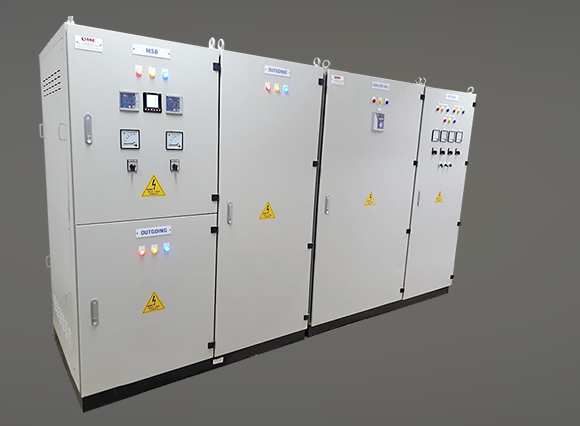
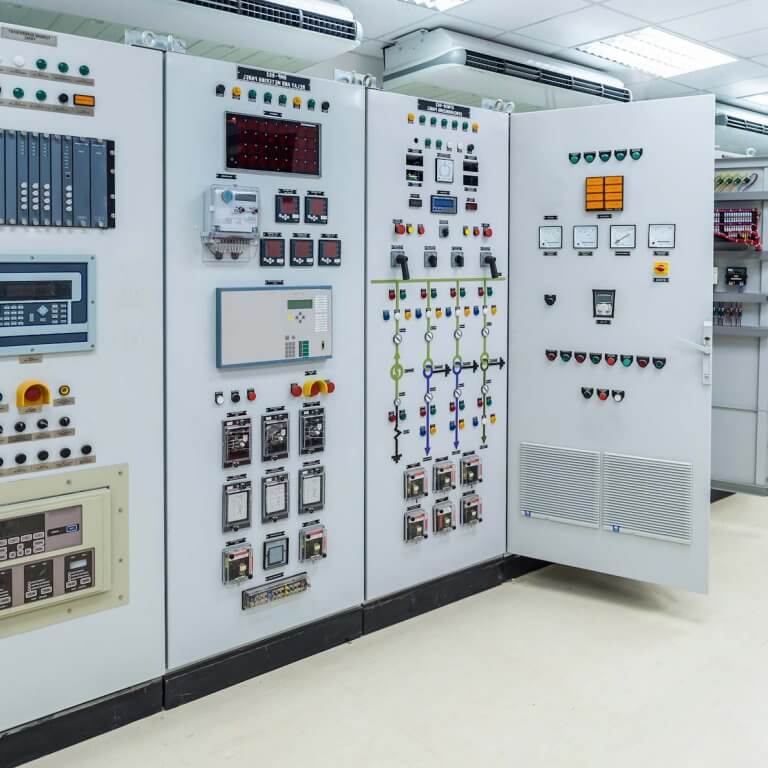
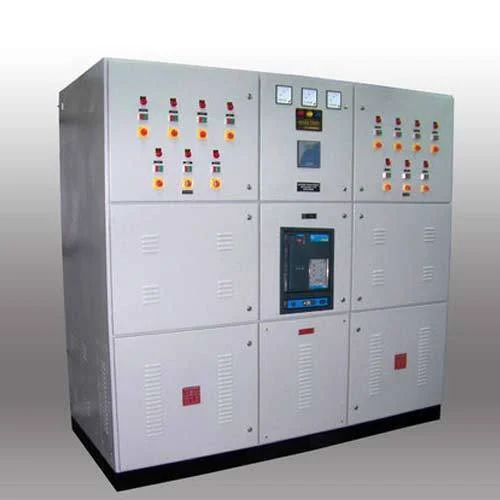
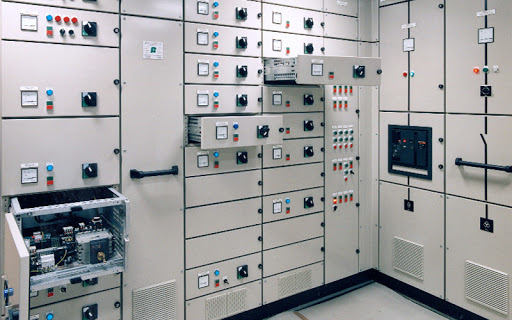
WHAT IS A FACTORY CONTROL CABINET?
A factory control cabinet, commonly found in industrial settings, is an essential component that houses control systems for various machinery and processes. It contains the necessary electrical hardware and control equipment, such as programmable logic controllers (PLCs), power distribution components, and other automation devices. These cabinets are designed to organize and protect this equipment, ensuring the safe and efficient operation of industrial machinery. They often include features like temperature control and are built to withstand harsh industrial environments. Control cabinets play a pivotal role in streamlining and managing the complex operations within a factory.
WHAT ARE THE BENEFITS OF A FACTORY CONTROL CABINET?
Centralized Control
Cabinets consolidate all controls for machines and processes into a single location, allowing for easier operator monitoring and adjustment. This simplifies operations and leads to improved efficiency.
Reduced Electrical Hazards
Cabinets enclose and organize electrical components, protecting workers from accidental contact with live wires and preventing shocks or fires. This improves safety and peace of mind in the workplace.
Safety and Protection
Offers protection for essential control equipment like PLCs and power components, safeguarding against environmental factors and reducing risk of damage.
Reduced Costs
Improved efficiency, reduced downtime, and extended equipment life can lead to significant cost savings over time.
ELECTRICAL CONTROL CABINET – OPTIMAL PRODUCTION SOLUTION
APPLICATION OF FACTORY CONTROL CABINETS IN PRODUCTION
Factory control cabinets are widely used in production to streamline and enhance industrial processes. Their applications include:
- Managing Machinery: Control cabinets regulate and monitor machinery operation, ensuring efficiency and safety.
- Automated Processes: They facilitate automated production lines, reducing manual intervention and errors.
- Monitoring Systems: Provide real-time data on equipment performance and production output, enabling proactive maintenance and optimization of operations.
- Integration of Various Controls: They integrate different control systems, such as temperature, pressure, and motion controls, for seamless operation.
WHY SHOULD YOU USE FACTORY CONDITIONED ELECTRICAL CABINETS IN PRODUCTION?
Guaranteed Quality and Safety
Factory-conditioned cabinets undergo rigorous quality control checks and are built to meet stringent industry standards. This ensures they’re constructed with durable materials, have robust welds, and possess the necessary certifications for electrical safety. Think of it as buying a car that’s already been through a pre-purchase inspection – peace of mind guaranteed.
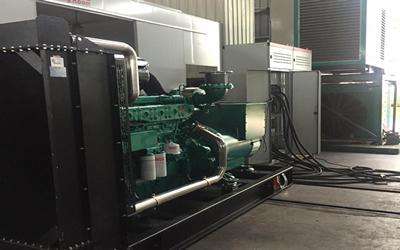
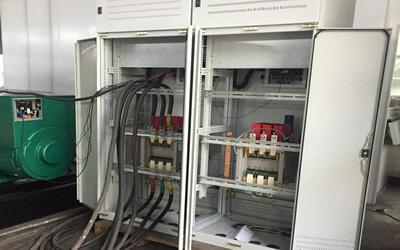
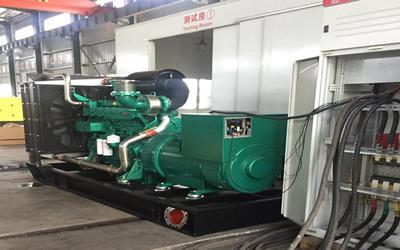
Customization Options
While pre-assembled, factory-conditioned cabinets do offer flexibility for customization. You can choose from various sizes, configurations, and add-ons like cooling units or HMI panels to tailor the cabinet to your specific needs. This ensures optimal functionality and integration within your existing production setup.
Cost-Effectiveness in the Long Run
The initial investment in factory-conditioned cabinets might seem higher compared to building your own or opting for cheaper alternatives. However, consider the hidden costs. Factory-built cabinets save you time, labor, and potential material wastage. Their superior quality translates to longer lifespans, reduced maintenance needs, and minimized downtime. In the long run, they prove to be a cost-effective and reliable solution.
Making the Smart Choice
ELECTRICAL CONTROL CABINETS – REASONABLE PRODUCTION PROCESS
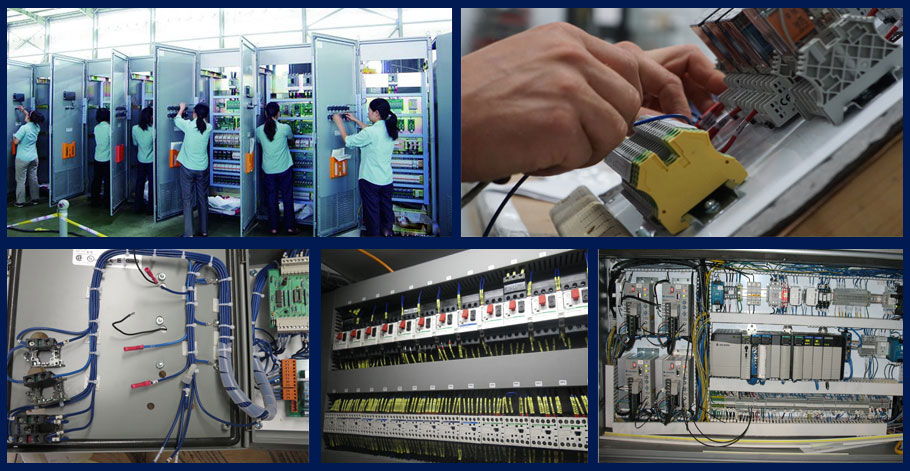
NOTES WHEN USING THE FACTORY CONTROL CABINET
Regular Maintenance: Regularly inspect and maintain the cabinet to ensure optimal functionality.
Proper Installation: Ensure it is correctly installed and grounded to avoid electrical hazards.
Environmental Considerations: Be aware of the environmental conditions to prevent overheating and moisture-related issues.
Safety Compliance: Adhere to safety standards and regulations for electrical systems.
Clear Labeling: Clearly label all components for ease of use and troubleshooting.
Secure Access: Limit access to authorized personnel to prevent accidental damage or mishandling.
WHY DO CUSTOMERS CHOOSE VNATECH?
With over 10 years of experience in the field of manufacturing, installation and distribution of machinery and equipment as well as production systems for industrial plants, we affirm that we will bring customers quality products. best quality and service. Vnatech’s Andon systems are confident that they will meet the technology, professionalism and experience requirements for all customers in all manufacturing fields.
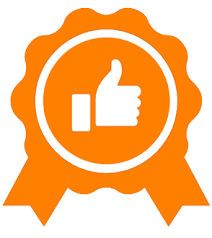
Quality
Vnatech commits that all of our products meet quality requirements when delivered to customers
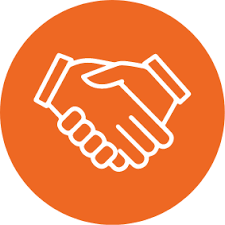
Reputation
With more than 10 years in the field of manufacturing, installing machinery and equipment and designing systems for the factory, Vnatech is a reputable and trustworthy address.
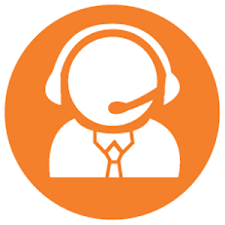
Good service
Coming to Vnatech, you will always be warmly welcomed by the staff, given complete, accurate and quick information and positive after-sales services.
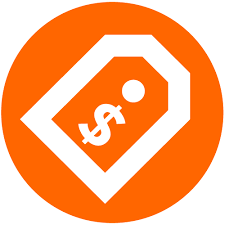
Reasonable price
Our products and components are imported directly from large, reputable manufacturers, without going through third parties, so they always have the most competitive prices.